Next: Frontiers in Advanced Manufacturing
The human impact of all other fields of applied science depends, in the end, on advanced manufacturing. Every translational innovation requires something—a smart device, a novel material, a drug molecule—to be produced reliably, safely, and affordably at scale. Making that happen is the domain of manufacturing scientists and engineers.
One of several NSF-sponsored Industry/University Cooperative Research Centers across UMass, the Center for Science of Heterogeneous Additive Printing of 3D Materials (SHAP3D) at UMass Lowell works to advance additive manufacturing techniques like 3D printing. With an eye on the needs of industry, SHAP3D develops methods for additively printing varied products with a range of functions through the integration of advanced materials, complex structures, and cutting-edge processes. Partners include major manufacturing companies like Raytheon, Greene-Tweed, HP, and Stratasys; small businesses like Hutchinson, K&C, and Integrity; government entities, such as the U.S. Army Combat Capabilities Development Command; and researchers at the University of Connecticut and Georgia Tech.
Leading the global innovation economy demands excellence in advanced manufacturing. The United States has made significant investments in building its capacity for cutting-edge manufacturing, including the launch of the National Network for Manufacturing Innovation—now Manufacturing USA—in 2014. These investments pay important dividends well beyond bringing next-generation products and therapies to market; advanced manufacturing has real implications for the security of US intellectual property, our resiliency and independence from other nations, and our prosperity. Manufacturing is among the top five US job producers— employing 11.7 million people in 2018. Six trillion dollars of goods were shipped from US manufacturers in 2018.
Massachusetts has a long history in manufacturing, dating back to the water-powered technologies of the 18th century. The New England Council’s report “Advanced to Advantageous” makes the case that the region is poised today to lead advanced manufacturing’s “next wave” of innovation, spurred by disruptive technologies like additive manufacturing and the Internet of Things. That leadership is recognized at the federal level: In November 2020, the Department of Defense awarded Massachusetts a $3.2 million grant to create a national model for training manufacturing technicians with skills needed by Manufacturing USA Institutes.
The Commonwealth’s interest in advanced manufacturing—a sector that directly supports the both the state’s vaunted innovation economy and its workforce—is reflected in industrydriven and industry-focused programs such as Mass MEP, MassTech, the Advanced Manufacturing Consortium, the Massachusetts Manufacturing Innovation Initiative, Advanced Manufacturing Training grants, Advanced Manufacturing Summits, and in the UMass system itself.
The University has been active in manufacturing research since the 1950s. As advanced manufacturing has increased in importance, the campuses have moved into a commanding position, due to faculty expertise in a wide range of manufacturing processes and systems, and in complementary fields like materials science, artificial intelligence, robotics, and data science. Today, we are one of the nation’s premier institutions in terms of industrialscale facilities for additive, roll-to-roll, biomedical, nano-, composites, and plastics manufacturing; the state’s top producer of trained workers in this field; and a strong partner to industry in every aspect of advanced manufacturing.
Big Ideas
UMass campuses are guiding America’s manufacturing renaissance as university partners in eight of the country’s fifteen Manufacturing USA Institutes. Manufacturing USA, sponsored by the Departments of Commerce, Defense, and Energy, encourages manufacturing innovation and industry-university-government collaboration. UMass research is supported by state-of-the-art facilities that include roll-to-roll fabrication, additive manufacturing, and biomanufacturing, providing a unique set of custom tools for the translation of advanced materials and nanomanufacturing processes to industrially relevant, scalable manufacturing platforms.
Anyone tested for COVID-19 in the US has likely encountered UMass manufacturing technology at the end of a nasal swab. Puritan Medical Products’ flocked swabs—developed with UMass Dartmouth bioengineering professors Yong Kim and Armand Lewis—are FDA preferred for COVID tests due to their coronavirus collecting efficiency, which reduces false negatives. With $126.7 million in government funding, the Maine-based company has opened two new plants since April, increasing swab production from 1 million to 90 million per month.
Today’s strengths
Today, UMass is innovating in five areas that represent the forefront of modern manufacturing.
Additive manufacturing
The rise of additive manufacturing processes like 3D printing represents a new paradigm for the manufacturing industry, one focused on customization and innovation. Additive processes build products in layers according to precise computer models, and offer appealing advantages to industry: Less waste, more flexibility, easier prototyping, and the ability to produce small lots cost-effectively. Additive manufacturing was an $11.8 billion industry in 2020 (a 21 percent jump over 2019) and is projected to grow to $53 billion by 2029.
Additive manufacturing research at UMass spans all aspects of the modern industrial process—including modeling, production technologies, quality-control automation, information systems architecture, and data-driven predictive analytics— and is highly collaborative with government and industry. The Raytheon-UMass Lowell Research Institute, for example, is an academiccorporate research partnership where Raytheon engineers work closely with UMass faculty on internal and government-funded research projects developing additive manufacturing for defense electronics. UMass Lowell has also established the Printed Electronics Research Collaborative to expand corporate partnerships to include companies developing the supply chain for printed electronics.
UMass is a tier-one member of NextFlex, a national Manufacturing Innovation Institute focused on flexible hybrid electronics, and two National Science Foundation (NSF) Industry/University Cooperative Research Centers in this field: SHAP3D (3D printing) and the Center for e-Design (additive substrate characterization and prediction). Both are highly focused on research projects with immediate industrial impact.
SHAP3D-affiliated faculty members Dave Kazmer and Chris Hansen, for example, invented an additive system that can print two different materials on demand, making it possible to print core/sheath materials and gradient materials—a capability that didn’t exist before. Researchers with the Center for e-Design, which operates a 2,500 square foot computing facility with state-of-the-art modeling, simulations, and engineering software, collaborated with Raytheon to produce a co-copyrighted software tool that helps product designers tell whether additive manufacturing is the right process for their project. Scientists in UMass Amherst’s Multiscale Materials and Manufacturing Laboratory are working with the Department of Energy to develop optimal 3D-printed structures for batteries and other energy storage devices.
These researchers can draw on the Advanced Digital Design and Fabrication core facility, part of the $150 million Institute for Applied Life Sciences at UMass Amherst, which operates cutting-edge, industrialgrade, additive equipment. It is a production hub for the flagship campus and firms throughout the state, and a springboard for local industry development.
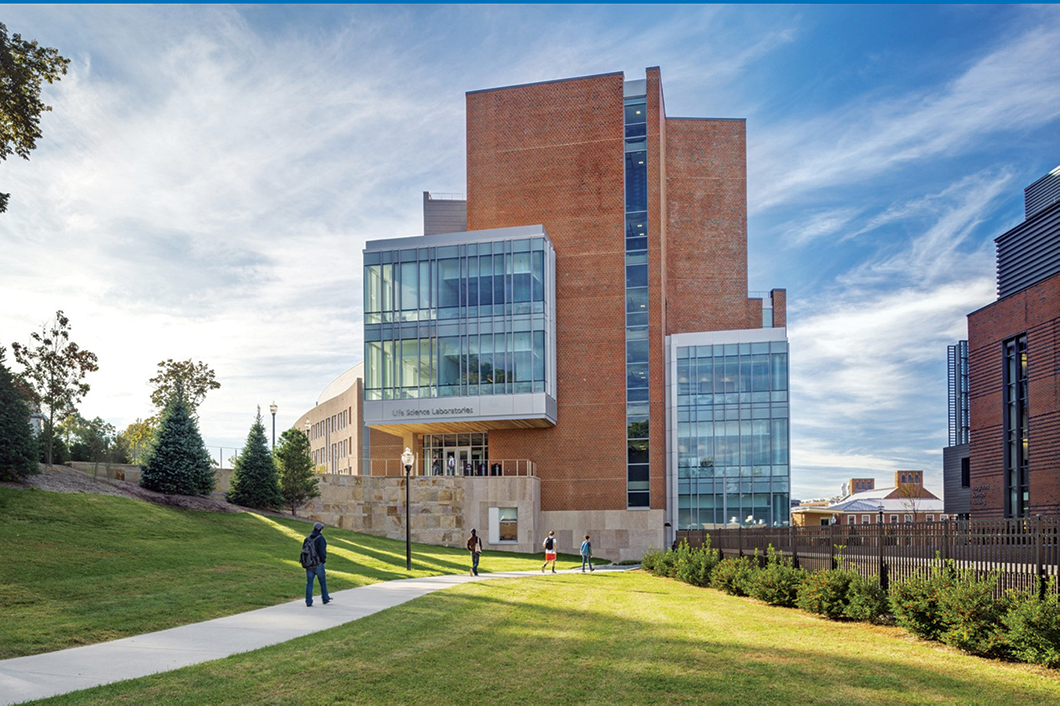
Materials in manufacturing
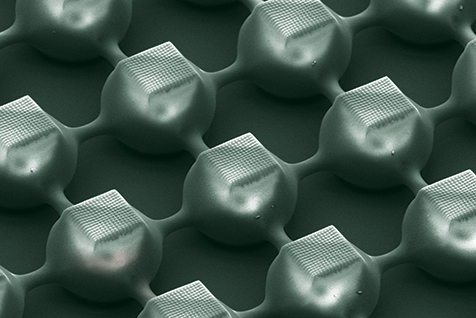
UMass has longstanding strength at the intersection of materials science and manufacturing, in both developing and producing new materials that resolve vexing problems and in analyzing how materials behave at scale. UMass Amherst’s Center for UMass-Industry Research on Polymers, the longest-running NSF Industry/University Cooperative Research Center in the nation, has been working in this space since 1980. The system was an early leader in nanomaterials manufacturing. UMass Lowell and UMass Amherst hosted two of the first four NSF Nanoscale Science and Engineering Centers focused on nanomanufacturing: the $24.5 million Center for High-Rate Nanomanufacturing (and its affiliated $5 million state-supported Nanomanufacturing Center of Excellence), and the $36 million Center for Hierarchical Manufacturing.
UMass Dartmouth’s high-speed video camera shoots 10 million frames per second—that’s one exposure every 50 nanoseconds—to capture in minute detail how additive manufacturing substrates, bones, and other materials stress and break. Understanding microsecond-long events like fast propagating cracks is key to creating more resilient materials.
The Lowell campus hosts the largest university-based collection of polymer processing equipment in the United States.
Research groups across the system are creating materials with a wealth of valuable properties. UMass Dartmouth faculty, for instance, hold a number of patents related to fiber-based energy-absorbent materials (used, for example, to reduce rotational effects of impact in sports helmets).
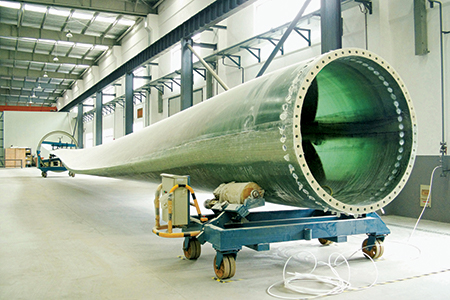
UMass Lowell’s Advanced Composites and Textiles Research Lab has an international reputation for its research on the manufacturing of textile reinforced composites, which are widely used for wind turbine blades and are increasingly used in the aerospace and automotive industries (as fuel-saving, low-weight alternatives to aluminum and steel) and in the defense industry (for helmets to protect vehicles against roadside bombs and artillery). Through NextFlex, UMass Lowell faculty have also invented flexible substrates for tunable antennas that can fit into smaller, lighter electronics.
Amherst engineers have manufactured multi-scale materials—which, like many natural materials, combine macro-, micro-, and nanoscale structures—to create super waterrepellent surfaces and, with the Army Research Lab, lightweight body armor that directs fracturing at the nanoscale.
On the flip side, chemists in UMass Boston’s Center for Green Chemistry are removing materials from manufacturing, reducing or eliminating the use or creation of hazardous substances in the production of chemical products.
Biomedical manufacturing
Biomedical manufacturing, the manufacturing of drugs and medical devices, is a vital step in any medical advance’s journey from the bench top to the bedside. The UMass system has strength in many aspects of the field.
One key focus is the use of genetically modified living cells as factories to create biopharmaceuticals. UMass Lowell hosts one of five sites of the national Advanced Mammalian Biomanufacturing Innovation Center (AMBIC), an NSF Industry/ University Collaborative Research Center for biomanufacturing, and the Massachusetts Biomanufacturing Center, a research and consulting group that helps biopharmaceutical companies in the state meet their manufacturing needs.
AMBIC works to make biopharmaceutical manufacturing processes more efficient and costeffective by bringing together leaders from industry, academia, and government to foster upstream mammalian cell culture innovation. One example: AMBIC is developing a baseline reference cell culture platform for biomanufacturing, which currently depends on a variety of Chinese hamster ovary cell strains as the principal platform for producing the great majority of the world’s biopharmaceuticals. AMBIC’s standardized platform will facilitate understanding of cells and cell culture processes in a way that is impossible today, given the diversity of cell lines and media used.
The UMass Medical School and UMass Lowell are members of the National Institute for Innovation in Manufacturing Biopharmaceuticals, a Manufacturing USA Institute focused on accelerating innovation in biomanufacturing. The medical school also oversees MassBiologics, which has state-of-the-art facilities producing licensed therapeutics, investigational drug substances, monoclonal antibodies, and vectored therapeutics, and has brought more than 20 licensed products, including some critical vaccines, to market.
Many faculty across the system are working on the manufacture of medical devices. One hub for this work is the Center for Personalized Health Monitoring, part of UMass Amherst’s Institute for Applied Life Sciences. Center researchers are developing and commercializing wearable, wireless sensors for health monitoring, manufactured on flexible sensor platforms. These devices continuously collect valuable data on heart rate, blood pressure, and other vital signs, providing physicians with more accurate information on a patient’s condition than occasional office visits reveal.
Other medical device thrusts across the system include photonics equipment for biological applications, manufacturing components for soft robotics and rehabilitation robotics (including lower-leg prosthetics that power steps the way a living leg would), exoskeletons, and other therapeutic robots. Functional fabrics imbued with sensors that can send health information to doctors, anti-biofouling coatings that prevent bacteria from sticking to medical instruments, and a wearable, wireless biosensor system for remote detection of life-threatening events in newborns—these are just some of the inventions that were born in faculty labs.
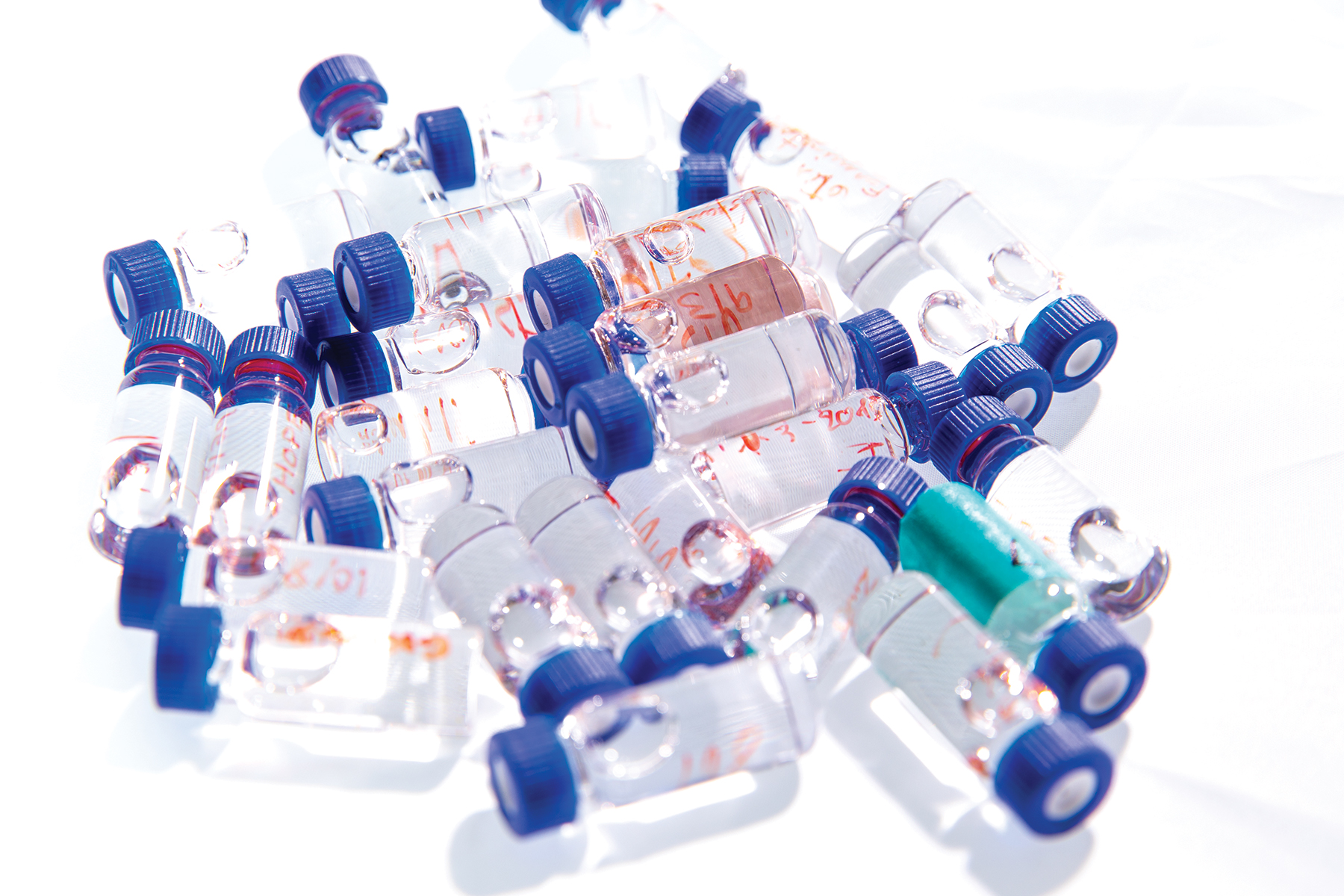
The work of biomedical manufacturing researchers has been critical in the fight against COVID-19, including research into antiviral coatings and filtration materials for reusable personal protective equipment, testing swabs made with UMass Dartmouth’s patented flocking technology, and low-cost, fast-track face shields designed in collaboration with nursing faculty.
Soldiers are trained to endure stressful situations, but they are not immune to the toll pressure takes on concentration, emotional regulation, and decision-making. UMass Amherst polymer scientist James Watkins, in collaboration with General Electric and the US Air Force, is developing a roll-to-roll manufactured wearable biosensor that can monitor a soldier’s stress level and detect potentially problematic agitation. The sensors—flexible, Band-Aid-sized patches potentially produced for less than $1 each—sense stress- and fatigue-related chemicals in the wearer’s sweat and transmit the data wirelessly to monitors.
Roll-to-roll manufacturing
Advanced roll-to-roll manufacturing—a process that coats, prints, embeds, or laminates materials onto flexible plastics or textiles wound on rollers— underpins the production of flexible and wearable electronics and nano-printing for repellent surfaces, nanoscale electronics, sensors, batteries, fuel cell membranes, and more. Industry analysts predict that the total market for printed, flexible and organic electronics—many produced with advanced roll-to-roll technology— will grow from $31.7 billion in 2018 to $77.3 billion by 2029.
UMass has a deep strength in roll-to-roll manufacturing research, particularly where it intersects polymer science and nanotechnology. The system operates industrial-scale roll-to-roll production facilities on two campuses, at the UMass Amherst Center for Hierarchical Manufacturing’s $25 million Roll-to-Roll Fabrication and Processing Facility, and UMass Lowell’s Advanced Manufacturing of Polymers and Soft Materials Center and the Fabric Discovery Center. (Production services are offered to companies in their region.)
_Edwin%20Aguirre_IMG_4036.jpg)
The UMass Amherst Department of Polymer Science and Engineering— one of the largest academic centers for polymer research in the world, staffed by faculty leaders in a number of fields—is funded by more than forty companies and government agencies. Professor Tom Russell is a National Academy of Engineering member well known for the application of polymers to self-assembled devices. The department’s faculty has led the development of roll-to-roll advanced nanomanufacturing, a technology that is foundational to the department’s research in electronic, energy, and optical devices.
The UMass Lowell Plastics Engineering Department is an internationally recognized leader in plastics engineering education, offering the first and largest accredited plastics engineering program in the U.S. The affiliated Center for Advanced Manufacturing of Polymers and Soft Materials combines this strong plastics heritage with industrial scale equipment to develop advanced nanomanufacturing processes for both plastics and elastic polymers (elastomers).
UMass Lowell has unique capability in producing elastomers for stretchable electronics, and is home to one of three student chapters of the Rubber Division of the American Chemical Society. Lowell also houses the NSF Center for High-rate Nanomanufacturing. Joint research includes the development of roll-to-roll techniques for production of nanostructured liquid-proof surfaces and nanoscale patterning of polymer blends.
In less than two weeks in April 2020, a team of engineering and nursing faculty from UMass Amherst designed and began producing face shields that can be quickly and cheaply mass-manufactured to meet COVID-related PPE needs. The team shared the design with manufacturers and donated 80,000 shields to first responders in the region.
Manufacturing automation
Supply chain prediction. Production line coordination. Equipment maintenance and monitoring. Quality control. For an advanced manufacturing operation to be successful, all these functions must integrate with and inform each other—no small management task. Manufacturing automation researchers at UMass are exploring how technologies like AI and machine learning, virtual and augmented reality, smart devices and the Internet of Things, data science, software engineering and computer modeling, and robotics can help companies coordinate these systems for maximum efficiency, accuracy, safety, and profit.
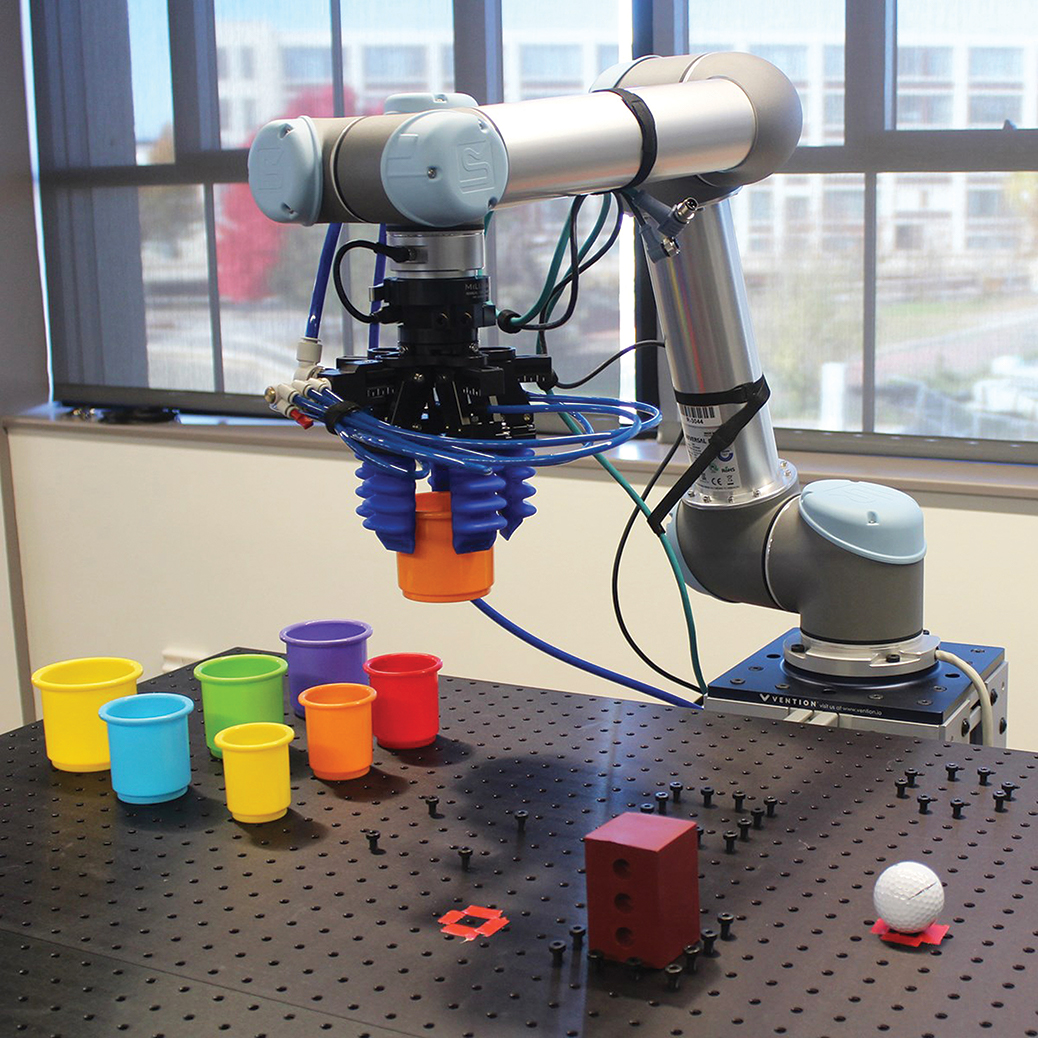
UMass Amherst’s Department of Mechanical and Industrial Engineering, host of the National Science Foundation’s Industry/University Cooperative Research Center for e-Design, develops manufacturing design paradigms and processes. The Dynamic Facilities Layout and Simulation Modeling Lab, the Human Robots Systems Lab, the Process Automation Lab, the Supply Chain Management Lab, and a number of other research groups whose work is relevant to manufacturing and automation collaborate to address virtually all aspects of automation.
Modeling and data fusion are particular areas of strength. Professor Ana Muriel, for example, works with aerospace manufacturer Pratt & Whitney to develop a detailed computer simulation, or “digital twin,” of the company’s supply chain to improve efficiency. Professor Sundar Krishnamurty works with the National Institute of Standards and Technology on compiling and coordinating actionable data from sensors on additive manufacturing equipment; and Professor Leo Liu studies integration of electronics, rubber components, and liquid metal technology in smart medical devices and micro-robots.
Tomorrow’s frontiers
Demand for custom products is growing. COVID-19-related shortages revealed the worrisome limitations of existing supply chains. Responsible resource management is essential. The future will require manufacturing innovations that support customization, are sustainable, and can rapidly pivot to manufacture what is needed at the moment. UMass is poised to move manufacturing toward that future over the next decade in the following areas:
Next frontier 1: Agile, instant, customized, adaptive manufacturing
Manufacturing systems that respond quickly and seamlessly to customer demand also promise to increase profit and reduce waste for manufacturers. Creating highly responsive systems requires the integration of AI, robotics, modeling, and software engineering, as well as the materials and processes themselves.
Work toward this frontier is already underway at UMass: from postdoctoral research fellow Douglas Eddy’s use of predictive analytics to model product lifecycles to Professor Xian Du’s machine-learning-based models of roll-to-roll lithography (funded by an $580,000 NSF Faculty Early Career Development grant), to UMass Lowell’s multimaterial 3D printing that enables rapid change of material and product properties, as well as capacity for fully compounded rubber printing.
A related sub-frontier is the development of a manufacturing plan for pandemics, informed by our experiences helping manufacturers pivot to meet COVID-19-related PPE supply needs. UMass Lowell, along with MIT and Worcester Polytechnic Institute, represented academia on the Massachusetts Manufacturing Emergency Response Team, and subsequently received an NSF Future Manufacturing Networks grant to build on the lessons learned.
Next frontier 2: Green/Sustainable manufacturing
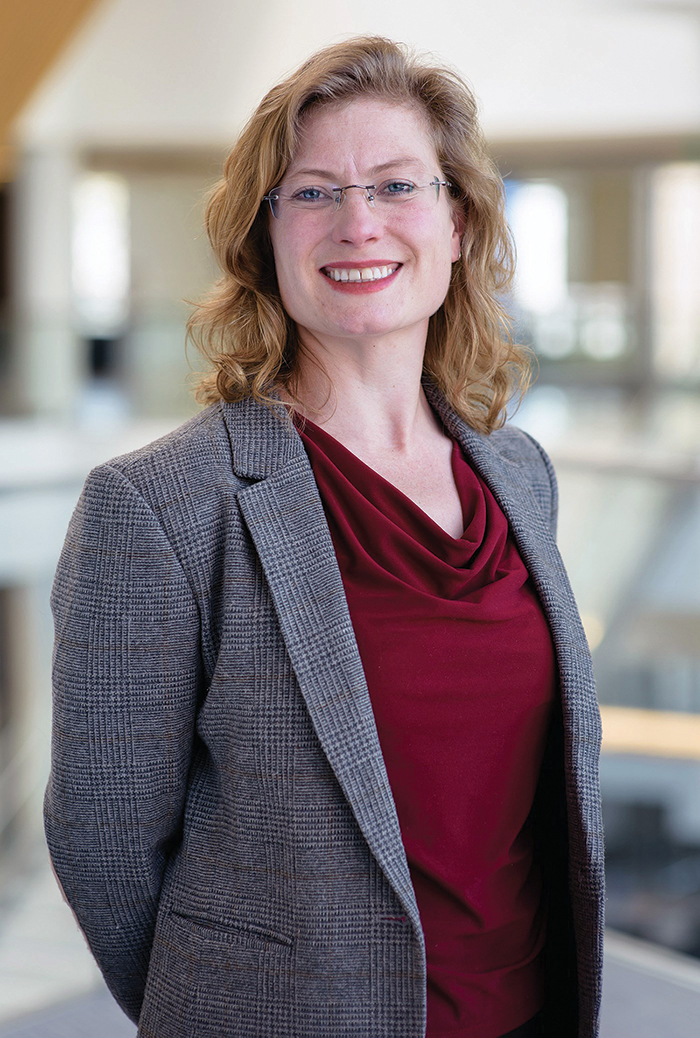
Sustainability is a critical imperative that cuts across all aspects of manufacturing. Over the next 10 years, UMass manufacturing scientists will be focusing more and more on creating products whose production does not harm the environment. As an active member of REMADE, the Manufacturing USA Institute for green manufacturing, UMass is already making advances in manufacturing sustainability, particularly in the creation and use of easily recycled and bio-based materials like the sustainable, tough, and damage sensing natural fiber composites developed by UMass Dartmouth professor Vijaya Chalivendra.
Manufacturing processes that render plastics more upcyclable—the goal of $2 million in Department of Energy funding at UMass Lowell—and systems that use engineered E. coli to break polyesters down into useful chemicals will leave the planet greener. UMass Boston’s Chemistry Department is developing waste-free (or low-waste) and energy-saving processes for the manufacturing of fine chemicals and pharmaceuticals, reducing fossil fuel use and emissions.
Next frontier 3: 3D printing on an industrial scale
3D printing, with its computer-powered nimbleness, is an essential element of an agile manufacturing industry. But today, additive manufacturing is not ready to grow to an industrial scale. The materials toolset is limited, for one, and throughput is too slow. One of the largest roadblocks is the lack of a uniform code of operation.
Additive manufacturing is the Wild West today, but UMass researchers are changing that. One important step: Sundar Krishnamurty, site director of UMass Amherst’s Center for e-Design, is working with the National Institute for Standards and Technology to develop standards and protocols for additive manufacturing that will yield consistent materials, processes, and results.
Next frontier 4: Integration of biological and non-biological manufacturing
Today, biomanufacturing is largely distinct from other aspects of manufacturing. But integrating the processes to create products that combine organic and inorganic materials is a frontier with health care applications that beg to be explored. UMass’s strengths in biopharmaceuticals, medical devices, wearable electronics, and advanced manufacturing puts us at a sweet spot for leading this integration.
Some of the manufacturing groundwork has already been laid. Nanomanufacturing is already highly bio-inspired; at UMass Lowell, for example, Joey Mead and Carol Barry have manufactured nano-patterned polymer surfaces that control interaction with biological materials and that could be used to create antibody-based sensors.
Next frontier 5: Collaborative robots in manufacturing
Co-robotics is a young field with big potential in manufacturing. Unlike today’s industrial robots, which are often cordoned off from workers for safety reasons, co-robots are designed to work alongside humans, safely and productively. The New England Robotics Validation and Experimentation Center at UMass Lowell is already evaluating collaborative robots for military and therapeutic use and is a natural partner for work on manufacturing co-robotics in the coming years.
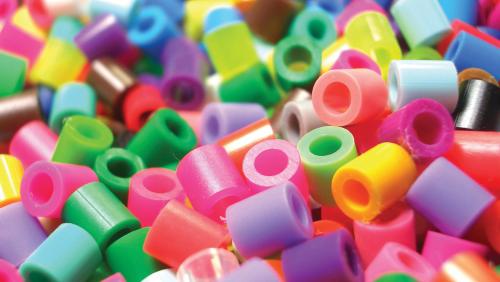
Bridging the advanced manufacturing workforce gap
More than 12 million Americans work in manufacturing, according the National Association of Manufacturers. The industry generates $2.35 trillion in the US each year and represents 62 percent of private-sector R&D. In 2020, almost 10 percent of the Commonwealth’s GDP ($53.26 billion) was produced by the manufacturing sector, which employs more than 6 percent of the state’s workers.
Approximately 718,000 of those manufacturing professionals comprise the highly skilled workforce of the state’s advanced manufacturers, the organizations responsible for producing the fruits of Massachusetts’ famed innovation economy. In 2015, advanced manufacturing was one of the Commonwealth’s three largest economic and employment sectors, according to the Massachusetts Department of Higher Education, which projected that the field would remain an important part of the Massachusetts economy for the foreseeable future.
At that time, however, the department’s data showed that demand for skilled advanced manufacturing professionals outstripped the state’s supply by 2 to 1. Industry projections today show that jobs in advanced manufacturing will grow by more than 5 percent over the next five years, and that advanced manufacturing employers will need to fill more than 74,000 jobs between now and 2030.
Where will the qualified candidates needed to bridge the advanced manufacturing workforce gap come from? The majority will graduate from the University of Massachusetts. In 2019, UMass awarded almost 20 percent of all related degrees conferred in the state, making the system the top producer of degree holders in our region.
At the UMass Lowell Center for High-rate Nanomanufacturing, professors Joey Mead and Carol Barry and their teams are developing superomniphobic and superhydrophobic surfaces, coatings and fibers that repel water, oils, and organic solvents due to micro- and nano-scale structures imparted during the manufacturing process. The potential applications are numerous: chemical protective clothing, self-cleaning fabrics and tents, anti-graffiti walls, surfaces that prevent growth of bacteria and other organisms, and smear-proof vehicle windshields, windows, and goggles are a few examples.
UMass degree completions in fields related to advanced manufacturing:
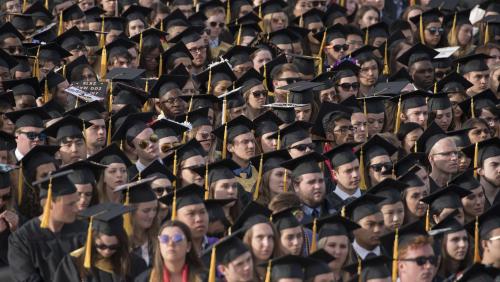
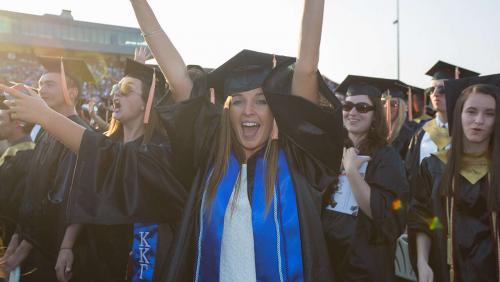
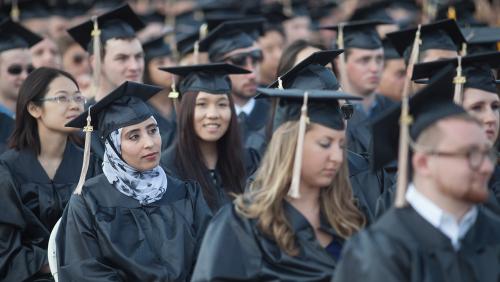
Massachusetts employment data in occupations related to advanced manufacturing:
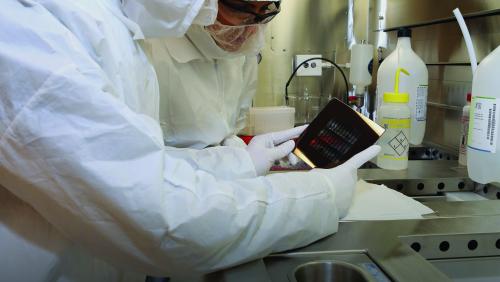
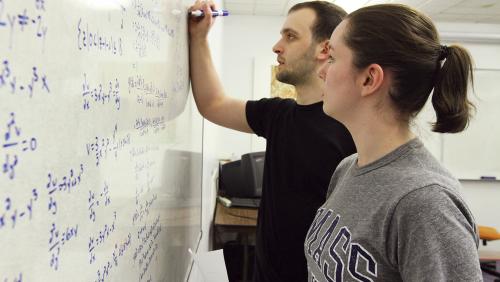
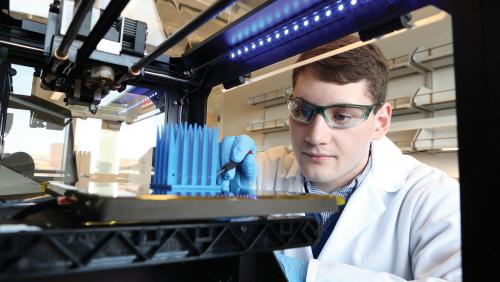
The University of Massachusetts’ faculty and students are passionate about the future they see for advanced manufacturing—an industry enabled by cutting-edge computing technology, rooted in sustainable practices, and producing a dizzying array of game-changing, life-saving products for health care, defense, and beyond.
We are proud of our place on the continuum of manufacturing excellence in Massachusetts, and of the contributions that excellence makes to the state’s standing and economy. Our mission, as the Commonwealth’s public university system, is to serve the state’s citizens, both by training the highly skilled advanced manufacturing workforce the state needs, and by supporting our industry partners through research, collaboration, and access to facilities.
Our manufacturing research is, by design, practical, industry-focused, and collaborative. The federal government has also prioritized building the nation’s advanced manufacturing capacity collaboratively, through public-private partnerships like Manufacturing USA. We remain an enthusiastic contributor to those efforts and look forward to expanding those partnerships in the future. Advanced manufacturing is the final, vital step in turning American innovation into American prosperity and global human impact. The University of Massachusetts will continue to rise to the challenge of making the advances of applied science reality.
Dig deeper
Advanced manufacturing research is happening in labs and centers across the University of Massachusetts. Visit the links below to find out more about some of the work going on across the state and the researchers conducting it.
Additive manufacturing
- ADDFab: Advanced Design and Fabrication core facility (Amherst) www.umass.edu/ials/addfab
- Printed Electronics Research Collaborative (Lowell) www.uml.edu/Research/PERC
- Raytheon-UMass Lowell Research Institute (Lowell) www.uml.edu/research/perc/ruri
- Center for e-Design NSF IUCRC (Amherst) edesign.ecs.umass.edu
- SHAP3D: Science of Heterogeneous Additive Printing of 3D Materials NSF IUCRC (Lowell)
- www.uml.edu/research/shap3d
- Flexible Hybrid Electronics: UMass Lowell NextFlex initiative (Lowell) www.uml.edu/research/nano/research/ flexible-electronics.aspx
- Multiscale Materials and Manufacturing Laboratory (Amherst) blogs.umass.edu/wenchen
Materials in manufacturing
- Center for UMass-Industry Research on Polymers (Amherst) www.umass.edu/cumirp/home
- Center for High-Rate Nanomanufacturing (Lowell) www.uml.edu/research/nano/chn
- Center for Green Chemistry (Boston) www.umb.edu/greenchemistry
Biomedical manufacturing
- Center for Personalized Health Monitoring (Amherst) www.umass.edu/cphm
- AMBIC: Advanced Mammalian Biomanufacturing Innovation Center NSF IUCRC (Lowell) www.ambic.org/university-of-massachusetts-lowell
- Massachusetts Biomanufacturing Center (Lowell) www.uml.edu/research/biomanufacturing
- National Institute for Innovation in Manufacturing Biopharmaceuticals (Lowell, Worcester) www.uml.edu/news/stories/2017/biopharmaceutical- institute.aspx
- MassBiologics www.umassmed.edu/massbiologics (Worcester)
- Biomedical Engineering and Biotechnology (Dartmouth) www.umassd.edu/engineering/graduate/ doctoral-degree-programs/biomedical-engineer- ing-and-biotechnolgy
Roll-to-roll manufacturing
- Polymer Science and Engineering Department (Amherst) www.pse.umass.edu
- Plastics Engineering Department (Lowell) www.uml.edu/engineering/plastics
- Center for Hierarchical Manufacturing (Amherst) chm.pse.umass.edu
- Center for Advanced Manufacturing of Polymers and Soft Materials (Lowell) www.uml.edu/research/nano
- Fabric Discovery Center (Lowell) www.uml.edu/research/fdc
- Roll-to-Roll Fabrication and Processing Core Facility (Amherst) www.umass.edu/ials/roll-to-roll-fabrication
Manufacturing automation
- NERVE Center (Lowell) www.uml.edu/research/nerve
- Mechanical and Industrial Engineering Department (Amherst) mie.umass.edu
- Dynamic Facilities Layout and Simulation Modeling Lab (Amherst) people.umass.edu/jmgsmith/lab/lab/software.htm
- Human Robots Systems Lab (Amherst) www.hrs-lab.org
- Supply Chain Management Lab (Amherst) www.ecs.umass.edu/mie/scmlab
Our thanks to the members of the advanced manufacturing faculty committee, who generously contributed their time and expertise to the creation of this report:
- Vijay Chalivendra, UMass Dartmouth (co-chair) Professor and Graduate Program Director, Mechanical Engineering
- Joey Mead, UMass Lowell (co-chair) Interim Associate Dean, Francis College of Engineering | University Professor, Plastics Engineering | Co-Director, Nanomanufacturing Center of Excellence | Deputy Director, NSF Center for High-rate Nanomanufacturing | Center Director, SHAP3D
- Wei Guo, UMass Lowell Associate Professor, Physics and Applied Physics
- Sundar Krishnamurty, UMass Amherst Professor and Department Head, Mechanical and Industrial Engineering | Director, Center for e-Design | Associate Director, Center for Personalized Health Monitoring